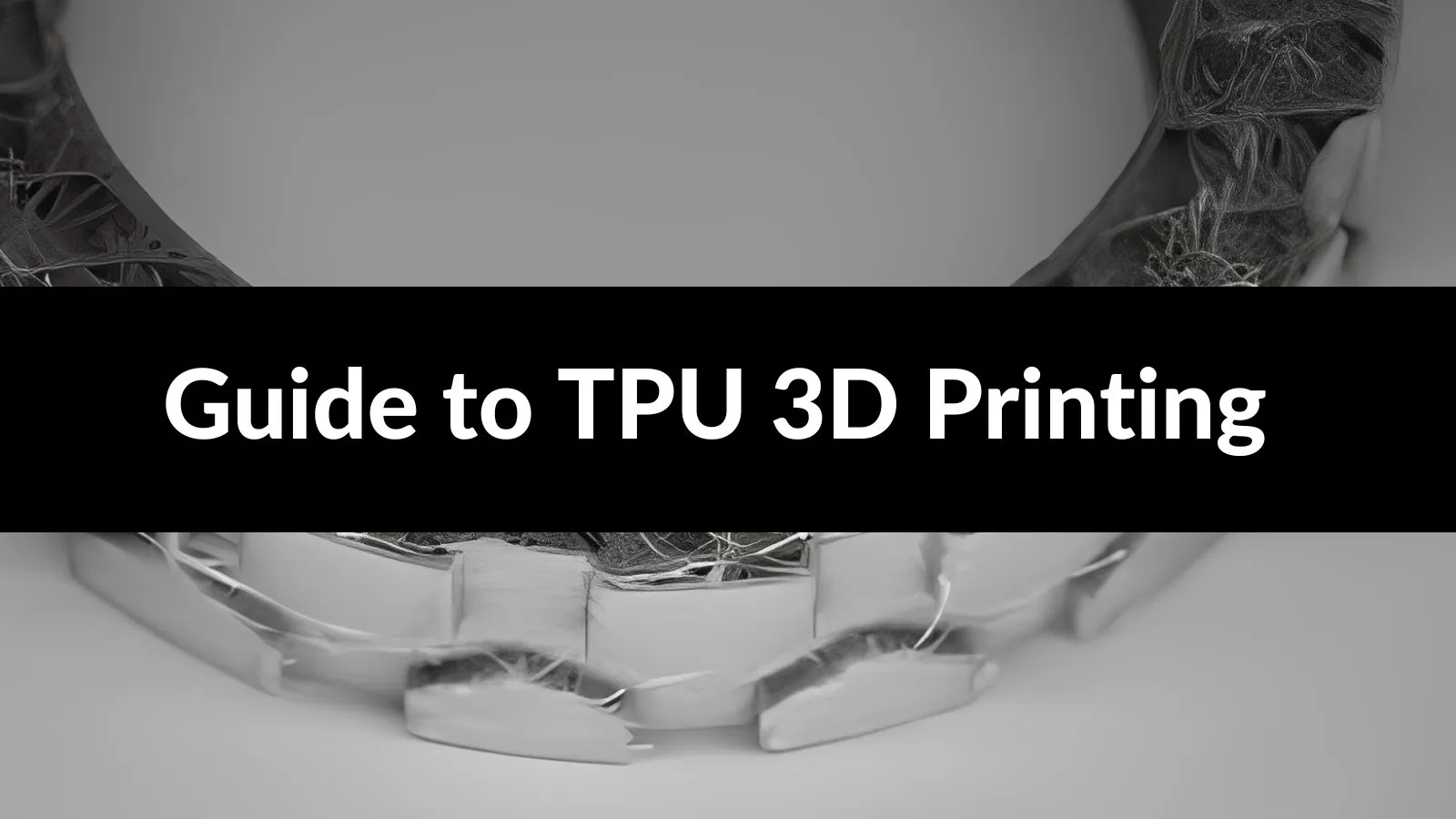
Thermoplastic Polyurethane (TPU) has become increasingly popular in 3D printing due to its unique combination of elasticity, toughness, and resistance to abrasion. TPU can be used to create objects that require flexibility while still maintaining their shape and strength. This guide provides an overview of TPU 3D printing, covering the material properties, printing parameters, and applications, offering essential insights for professionals looking to leverage this versatile material in additive manufacturing.
What is TPU?
Thermoplastic Polyurethane, commonly referred to as TPU, is a class of polyurethane plastics with many useful properties, including elasticity, transparency, and resistance to oil, grease, and abrasion. This material is a block copolymer consisting of alternating sequences of hard and soft segments. The hard segments provide strength and rigidity, whereas the soft segments contribute to the polymer’s elasticity and flexibility. Due to its unique molecular structure, TPU can be repeatedly stretched without permanently deforming its shape, making it an ideal material for various applications that demand durable flexing and bending.
TPU stands out in the world of 3D printing due to its bridging capabilities between rubbers and plastics. It offers the physical attributes of rubber such as flexibility and softness while also ensuring the processability of thermoplastics. This adaptable thermoplastic elastomer is well-suited for 3D printing because it can be easily processed through methods like Fused Deposition Modeling (FDM) or Selective Laser Sintering (SLS), yet retains its material characteristics post-printing.
The ability of TPU to withstand wear and tear alongside impacts makes it highly sought after for products requiring durability. As a result, when utilized in 3D printing processes, TPU opens up a world of possibilities for creating parts that need to perform under stress or flex while maintaining their original form.
How Are TPU Parts Made?
The fabrication of TPU parts using 3D printing technologies primarily involves two methods: Fused Deposition Modeling (FDM) and Selective Laser Sintering (SLS). In both processes, the object is printed layer by layer until it reaches the desired shape and size.
- FDM 3D Printing: In FDM 3D printing, a spool of TPU filament is fed into an extruder, which heats the material to its melting point. The molten TPU is then extruded through a nozzle that moves along specified coordinates. It cools down and solidifies quickly upon deposition, adhering to previous layers. This process necessitates precise control over the extrusion and platform temperatures, as well as careful calibration of print speed and retraction settings to minimize stringing or blobbing due to TPU’s elastic nature.
- SLS (Selective Laser Sintering) Method: On another front, SLS 3D printing employs a powder-based approach wherein a laser selectively fuses powdered TPU material according to the cross-sectional design of the object being produced. Each layer is fused on top of the previous one until completion. Afterward, any excess powder not sintered by the laser is removed from around the part, leaving behind only the solidified structure. Unlike FDM, this method does not require structural supports because unfused powder inherently supports overhanging features during production.
Why 3D Print TPU?
- Versatility: TPU is exceptionally flexible and durable, retaining its original shape even when stretched and flexed significantly.
- Resistance to Abrasion: TPU is highly resistant to abrasion, making it suitable for parts that experience significant wear and tear, resulting in cost savings on replacements.
- Resistance to Oils, Greases, and Chemicals: TPU’s resistance to oils, greases, and various chemicals makes it ideal for automotive parts and products exposed to harsh service environments.
- Color Customization: TPU can be colored during the production process, saving time and maintaining the uniform appearance of the printed item.
- Environmental Considerations: Certain grades of TPU are recyclable, making them more environmentally friendly compared to other plastics.
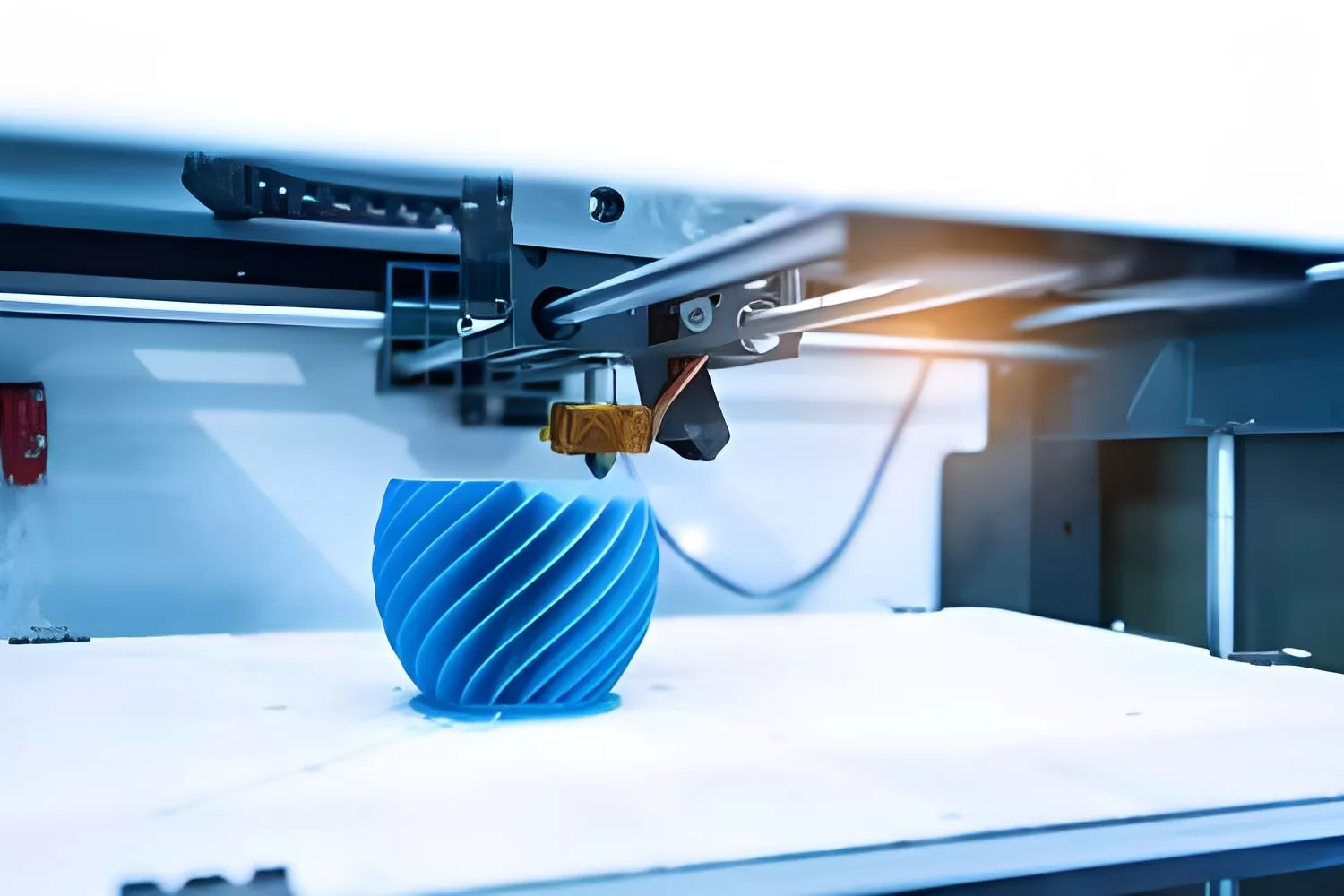
How to 3D Print With TPU
Method |
FDM 3D Printing | SLS 3D Printing |
---|---|---|
Overview | Widely used for TPU due to availability and ease of use in desktop printers | Popular for industrial applications, suitable for intricate parts |
Printing Process | Filament is melted and deposited layer by layer onto a build platform | High-powered lasers sinter powdered TPU together layer by layer |
Temperature | Nozzle temperature typically ranges between 220°C to 250°C | Requires precise temperature control in a specialized environment |
Print Speed | Slower print speeds can enhance adhesion between layers | No specific print speed considerations mentioned |
Retraction | Retraction settings should be calibrated carefully to avoid issues | No specific retraction considerations mentioned |
Equipment | Desktop printers are commonly used | Specialized equipment in professional settings |
Complexity | Relatively easy to set up and use | More complex due to temperature control and powder management |
Geometric Possibilities | Limited compared to SLS | Offers greater freedom for complex geometries |
Challenges | Elasticity of TPU can lead to clogging or stringing | Requires precise laser parameter tuning to avoid material degradation |
Output Quality | Proper settings can result in high-quality prints | Suitable for strong and complex parts |
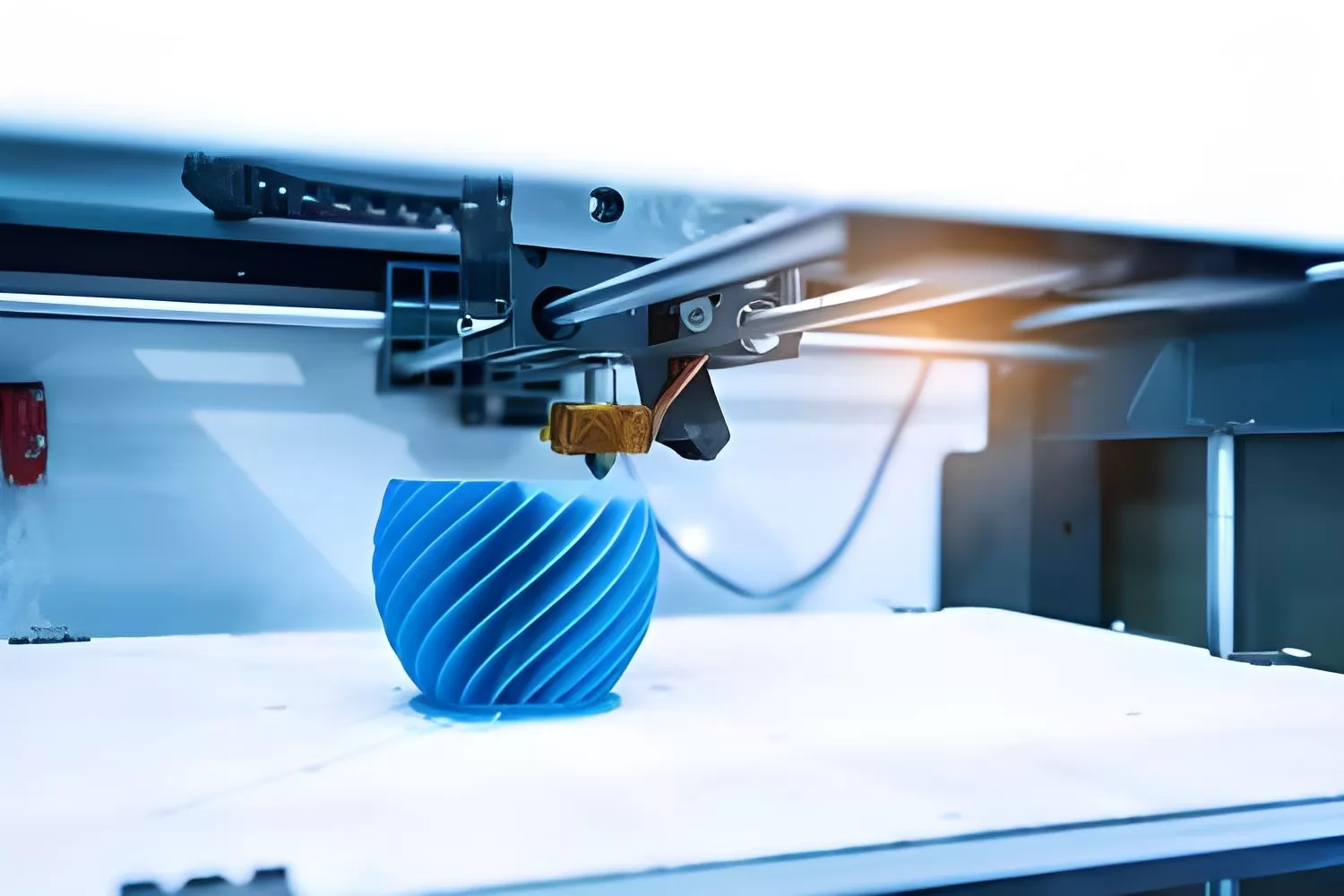
3D Printing TPU With FDM 3D Printing
This method involves the melting of a TPU filament by a heated nozzle, which then deposits the material layer by layer to create the desired object. The flexibility of TPU combined with the advantages of FDM technology makes it an attractive solution for creating parts that require elasticity or shock absorption.
To ensure success when 3D printing TPU with an FDM printer, a few critical parameters must be meticulously configured. Begin by selecting a direct-drive extruder, as this type will offer more consistent extrusion with flexible materials such as TPU due to its short path from the drive gear to the nozzle. Bowden extruders can also be used but may require fine-tuning since they involve a longer path that could lead to feeding issues.
The printing temperature plays a pivotal role in achieving optimal results. Generally, temperatures between 220-250°C provide good extrusion conditions for TPU filaments. However, exact temperatures may vary depending on the specific brand and grade of TPU material being used, so referencing manufacturer guidelines is recommended.
Print speed is another factor affecting print quality; a lower speed often yields better results when working with flexible filaments like TPU to allow more precise movements and reduce potential errors owing to the material’s pliability. Speeds around 15-30mm/s are commonly used for FDM printers when handling TPU.
Equally important is bed adhesion – ensuring that the first layer sticks well to avoid warping or shifting during printing. A heated bed at about 60°C paired with adhesive aids like glue or blue painter’s tape can assist in preventing issues related to adhesion.
Retraction settings should also be considered carefully because excessive retraction can lead to clogging given TPU’s flexibility. Aim for minimal retraction distance and speed settings suitable for your machine’s capabilities without causing oozing or stringing.
Ultimately, trial and error are part of perfecting the FDM 3D printing process with TPU due to its unique properties. Consistent testing and adjusting allow one not only to achieve successful prints but also to dial in on settings tailored for individual applications involving this robust yet malleable material.
3D Printing TPU With SLS 3D Printing
Selective Laser Sintering (SLS) is a sophisticated 3D printing technique typically associated with hard plastics like nylon, but it can also be adapted to print with Thermoplastic Polyurethane (TPU). This process involves using a high-powered laser to fuse small particles of TPU powder together, layer by layer, to build parts that are durable and flexible.
One of the most significant advantages of SLS 3D printing for TPU is its ability to produce complex geometries that are often challenging to create with FDM techniques. Since the TPU powder acts as its support material throughout the printing process, the likelihood of deformation or warping in intricate designs is significantly reduced. Additionally, parts produced through SLS have a consistent surface finish, which can be beneficial when the aesthetic quality and texture consistency are vital considerations.
Manufacturers and designers opting for SLS technology to print with TPU need to ensure proper temperature control within the print chamber since TPU’s sintering point is lower than more traditional SLS materials. An even distribution of thermal energy ensures that each layer fuses correctly without causing any unwanted distortions or discrepancies in mechanical properties.
When preparing for production, accessing fine-grained TPU powders conducive to laser sintering is critical. These powders allow for higher resolution in finished components and improve final product strength due to better fusion between powder particles during the sintering process.
Available TPU Materials
Thermoplastic Polyurethane (TPU) is available in a range of materials, tailored for 3D printing applications. The versatility of TPU extends to its varying degrees of hardness, measured on the Shore Hardness scale. Depending on the intended use, one can select from soft and flexible to more rigid grades of TPU. Several manufacturers offer TPU with different properties, such as enhanced UV resistance or flame retardancy.
The composition of TPU materials can also differ; some may be filled with additives that improve certain characteristics such as tensile strength or abrasion resistance. For instance, there are TPUs that contain fibrous fillers to enhance durability or metallic additives for magnetic properties. Such variations influence not only the performance but also the aesthetic outcome after the print is complete.
On the market, standard TPU filaments for Fused Deposition Modeling (FDM) 3D printing usually come in diameters of 1.75mm and 2.85mm, allowing them to be used across a wide variety of FDM printers. When considering Selective Laser Sintering (SLS), TPUs are provided in powder form and have specific particle size distributions optimized for this type of technology.
Compatibility with support structures varies among TPU types. Some have been designed to work seamlessly with soluble supports, simplifying the post-processing steps needed to achieve complex geometries without compromising the finish quality.
When selecting TPU material for a project, it’s crucial to consider not only mechanical properties and compatibility with your 3D printer but also factors like ease of printing and post-processing requirements. The range available ensures that there is an appropriate TPU material for virtually any application where a combination of flexibility and durability is desired.
Applications of TPU 3D Printing
Application | Description |
---|---|
Automotive Industry | TPU is used to create flexible car parts like air ducts, vibration dampeners, and protective covers due to its ability to withstand impacts and heat, ensuring long-term performance without deformation or degradation. |
Footwear Manufacturing | TPU is utilized to produce comfortable and durable shoe soles that can tolerate repeated bending and wear. It is also used in athletic apparel for supportive gear like knee braces and insoles that adapt to an individual’s anatomy. |
Medical Devices | TPU 3D printing is crucial for producing custom prosthetics, tubing for medical devices, and flexible hinges in the medical field, as it provides durability and biocompatibility required for such applications. |
Consumer Products | TPU is popular in consumer products, including smartphone cases known for their resilience against drops. It offers design flexibility with various colors and patterns. Additionally, it’s used in personal accessories like wearable wristbands and protective gear like goggles. |
Industrial Components | TPU is employed in creating complex industrial components that demand high-performance specifications and resilience. |
Customization and Resilience | TPU’s versatility makes it valuable in numerous sectors, offering customization options and resilience in a wide range of applications, from industrial parts to everyday items. |
Is TPU hard to 3D print?
Thermoplastic Polyurethane (TPU) presents a unique challenge in the field of 3D printing due to its inherent flexibility and elasticity. This material’s malleability is a stark contrast to the rigidity seen in more conventional printing materials, such as PLA or ABS. As TPU is softer and more pliable, the typical concerns during the printing process include difficulties with filament feeding and extrusion stability.
The elasticity of TPU can lead to complications when it is fed into the extruder. Without precise control, the filament may buckle or coil, causing jams or inconsistent extrusion rates. These potential issues necessitate specific settings and hardware adaptations: foremost among these are direct-drive extruders that minimize the distance between the drive gear and hot end—significantly reducing opportunities for misfeeds and snags.
Moreover, retraction settings require careful tuning to prevent stringing but not so much as to cause additional issues with filament transport. Printing speed must also be reduced; fast speeds could result in vibrations and poor layer adhesion, hence slower speeds maintain precision while successfully laying down layers of TPU.
Print bed adhesion is another hurdle yet surmountable with proper preparation and temperature control. Heated beds should typically be maintained within a narrow temperature range—usually around 30°C to 60°C—to promote adhesion without deforming delicate designs.
Admittedly, achieving optimal results with TPU depends on both a well-calibrated printer and an operator’s expertise. Understanding your machine’s capabilities, fine-tuning settings meticulously for each print job, and selecting appropriate filament types (with variations even within different grades of TPU) all contribute towards successful 3D prints with this versatile material.
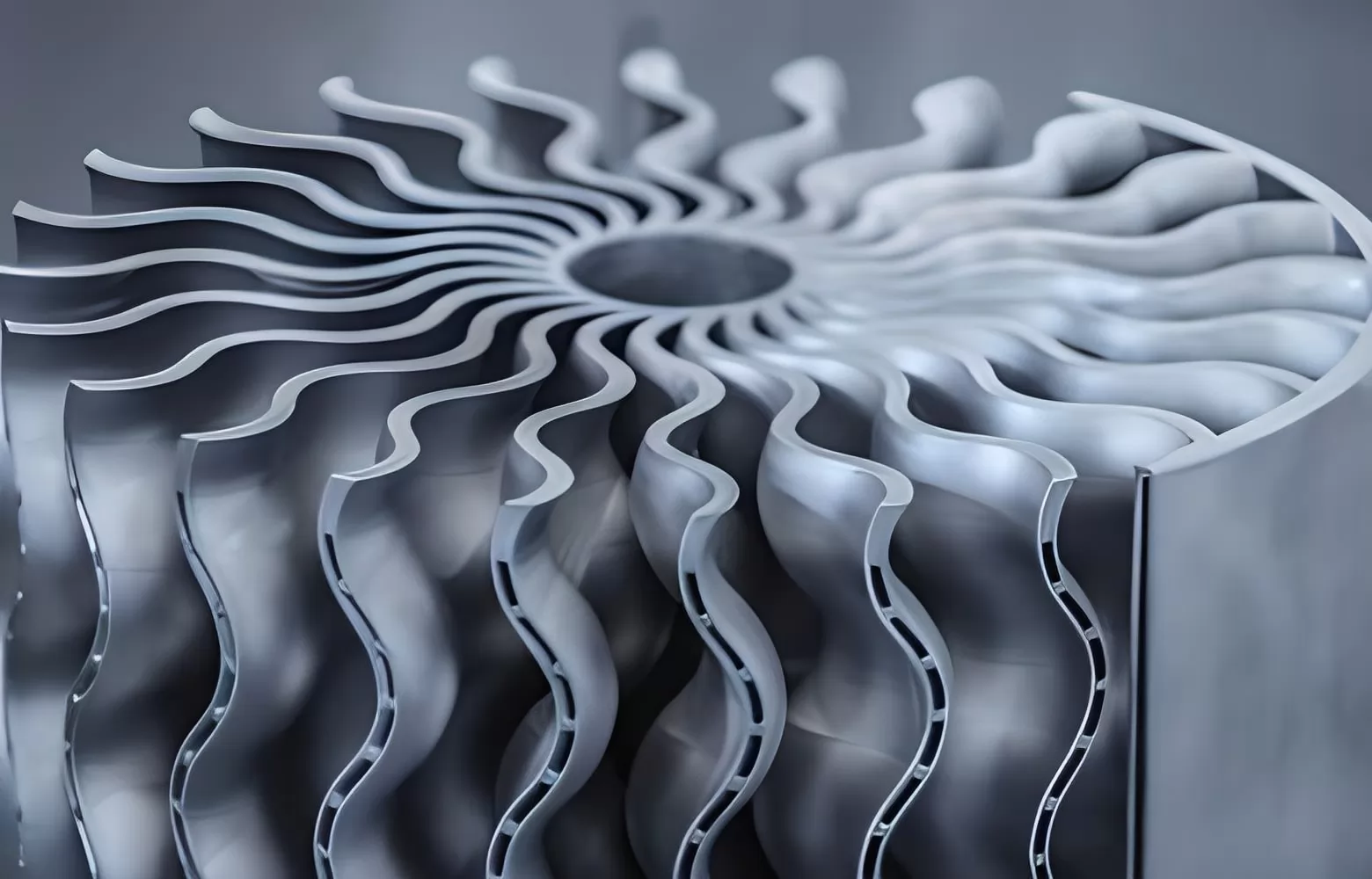
How to Successfully 3D Print TPU
Achieving success when 3D printing with Thermoplastic Polyurethane (TPU) requires attention to certain key factors.
Extruder Setup:
- Use a direct drive extruder to avoid issues with TPU’s flexibility.
- Adjust extruder tension correctly to prevent filament binding or buckling.
Temperature Settings:
- TPU typically melts between 225-250°C, but test to find the optimal temperature for your printer and TPU grade.
Print Speed:
- Reduce print speed to around 15-30 mm/s compared to stiffer filaments.
- Slower speeds ensure consistent extrusion and detail accuracy while preventing filament jamming.
Retraction Settings:
- Use conservative retraction settings to avoid clogging due to TPU’s elastic nature.
- Start with a low retraction distance and increment slowly based on test print results.
Adhesion:
- Ensure the build plate is leveled correctly.
- Consider using adhesives like glue sticks or blue painter’s tape if needed.
- Set bed temperature between 40-60°C for good first-layer adhesion without warping.
Top Layer Settings:
- Adjust top layers and infill percentage to provide structural integrity and material efficiency.
- Inadequate infill can lead to sagging in TPU.
Cooling Fans:
- Disable cooling fans during initial layers.
- Gradually turn them on during subsequent layers for better layer bonding and to prevent warping or deformities due to cooling.
By keeping these parameters in focus and adjusting them through trial and error if needed, one can reliably print complex parts with the versatile characteristic of thermoplastic polyurethane through 3D print technology.
What is the Easiest TPU to Print With?
When discussing thermoplastic polyurethane (TPU) for 3D printing, ease of use is an important factor to consider, especially for those new to working with flexible materials. Among the various grades of TPU available, some are designed to be more user-friendly and forgiving during the 3D printing process.
Generally, TPU filaments with a Shore Hardness around 95A are considered easier to print due to their balanced flexibility and stiffness. These materials offer a good compromise that allows them to feed through the printer without significant issues like clogging or jamming that can occur with softer TPUs. They also adhere well to the print bed and exhibit minimal warping or shrinkage, reducing the likelihood of print failures.
Additionally, higher-quality TPU brands often have tighter tolerances on filament diameter, which contributes to more consistent extrusion and better overall print quality. Choosing a well-known brand with positive reviews from other users can lead to a less complicated printing experience.
The printer’s hardware itself also plays a crucial role in facilitating easy TPU printing. Printers equipped with direct drive extruders generally handle TPU more efficiently than Bowden setups because the filament path is shorter and provides more controlled extrusion of flexible material.
Finally, it’s essential for individuals intending to 3D print with TPU to select settings optimized for such materials on their specific printers; this includes adjusting retraction settings, print speeds, and temperatures accordingly. Using a lower printing speed can greatly enhance success rates as it allows better precision when laying down each layer of material.
Selecting an appropriate type of TPU filament and optimizing your 3D printer setup accordingly can result in a smoother printing experience with fewer complications when working with this versatile but sometimes challenging material.
In Conclusion
In summary, TPU 3D printing presents a versatile option for creating flexible and durable parts, with unique considerations in print settings and material handling guiding successful prints.
Explore the dynamic world of TPU 3D printing today and unlock the potential for innovation in your designs. Contact us for more information on how to get started with this transformative technology or to purchase high-quality TPU filament tailored to your specific printing needs.